Une nouvelle fonctionnalité a vue le jour avec la nouvelle version SAP S4/HANA 1909 dans l’univers Manufacturing / PP Production Planning. Cette fonctionnalité s’appelle SAP pMRP Predictive Material and Resource Planning. Intégrée au sein du module PP (Production Planning), cette innovation transforme la manière dont les entreprises abordent la planification des matériaux et des ressources. En combinant des analyses avancées avec une interface utilisateur intuitive, SAP S/4HANA pMRP offre des insights précis et en temps réel pour optimiser les chaînes d’approvisionnement, réduire les coûts et améliorer l’efficacité opérationnelle. Dans cet article, nous explorons en profondeur comment cette fonctionnalité révolutionnaire permet aux entreprises de rester agiles et compétitives dans un marché en constante évolution.
SAP pMRP Predictive Material and Resource Planning – Introduction
Vue d’ensemble de pMRP
La fonctionnalité pMRP, ou Predictive Material and Resource Planning, est une des innovations clés de SAP S/4HANA. Conçue pour aider les entreprises à simuler, visualiser et ajuster pro activement leur planification de ressources et matériaux. Elle offre des prévisions précises et des recommandations de planification via des algorithmes avancés et une interface intuitive.
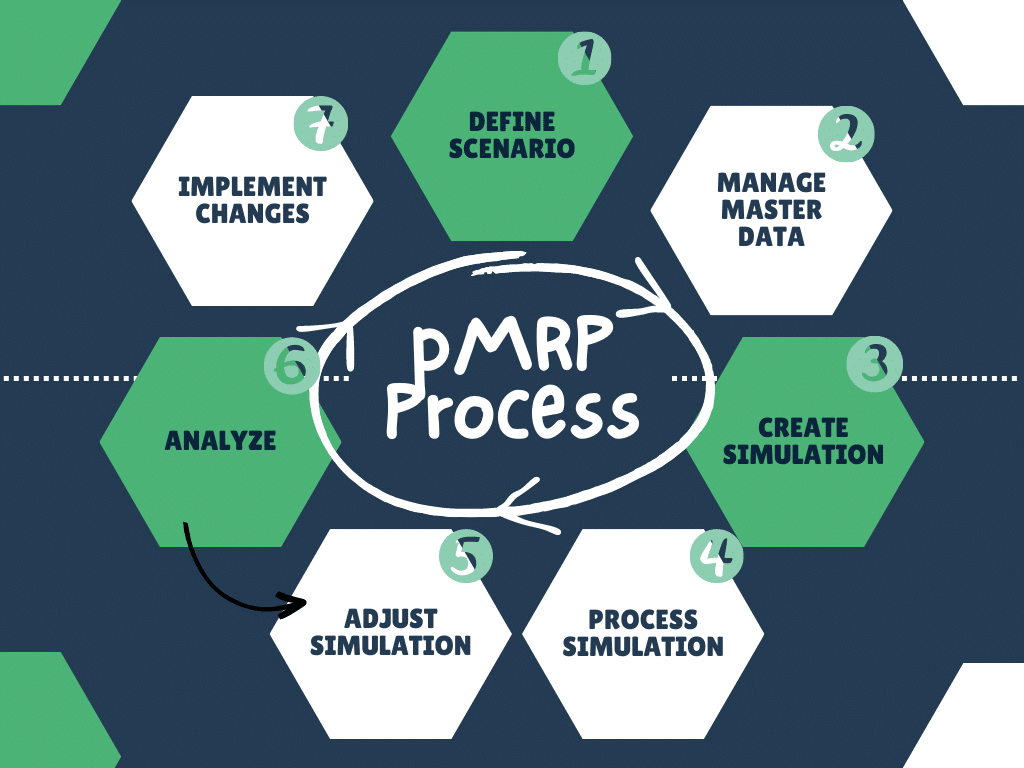
De plus, le module PP de SAP S/4HANA intègre étroitement pMRP, permettant ainsi une transition fluide entre la planification prédictive et la planification opérationnelle. Les données utilisées dans pMRP sont cohérentes avec celles du module PP, garantissant ainsi l’intégrité des données à travers les différentes phases de planification.
Le concept général de la fonctionnalité pMRP est similaire à celui de LTP Long Term Planning. En effet, pMRP peut être considéré comme le remplaçant de LTP, avec de nombreuses nouvelles fonctionnalités mais aussi une interface utilisateur plus ergonomique, notamment basé sur l’expérience utilisateur Fiori. En revanche, il est important de noter que LTP est une solution mature, alors que pMRP, bien que fonctionnel, reste en phase de développement. Ainsi, plusieurs nouveautés sont à prévoir avec les futures releases de SAP S4/HANA.
La fonctionnalité pMRP se base sur un plan de demande, reflété dans le système par des PIRs (Planned Independent Requirements). L’objectif principal est donc d’effectuer une analyse, en fonction du plan de demande, de la capacité des postes de travail. Le planificateur aura également la possibilité d’effectuer des simulations pour trouver le scénario idéal, tout en faisant des ajustements pour régler les problèmes de capacité des postes de travail. Enfin, après avoir effectué les ajustements nécessaires, on peut activer et transférer ceux-ci au planning opérationnel. Ainsi, les quantités modifiées viendront mettre à jour les PIRs.
pMRP ne requiert aucune configuration spécifique. En revanche, il est obligatoire de maintenir des données de base ainsi que des données transactionnelles pour pouvoir l’utiliser. Découvrons cela à travers la prochaine section.
Prérequis : données et configuration
En effet, pMRP peut être utilisé sans configuration supplémentaire que celles que le MRP classique impose : Plant, MRP Controllers etc… Par conséquent, si vous utilisez déjà la MRP classique, vous pouvez utiliser directement et sans configuration additionnelle la fonctionnalité pMRP. De plus, tout comme le MRP classique, pMRP nécessite la présence de l’utilisation de plusieurs types de données:
Gestion et exécution du pMRP
Fiori & pMRP
Comme introduit plus haut, la fonctionnalité pMRP est principalement accessible via l’expérience utilisateur Fiori. Avec l’utilisation de deux applications Fiori principales : Schedule pMRP Simulation Creation Fiori app & Process pMRP Simulations Fiori app. Les deux étants accessibles via SAP Fiori launchpad :
Note : Si les applications Fiori ne sont pas activées, vous pouvez le faire vous même en suivant ce tutoriel :
Tout d’abord, la première application Fiori Schedule pMRP Simulation Creation vous permettra, comme son nom l’indique, de créer la simulation. Tandis que la seconde, Process pMRP Simulations vous permettra d’exécuter et gérer la simulation.
Les grandes étapes
Etape n°1 : Création de la simulation pMRP
Cette première étape s’effectue avec l’application Fiori Schedule pMRP Simulation Creation. Il s’agit simplement de la création d’un background job.
Lors de cette première étape, le planificateur de production décide des données qu’il souhaite prendre en compte lors de sa simulation. Il faudra tout d’abord choisir entre deux options: Création des données pMRP via Top-Level Materials ou Création des données pMRP via Work Center. C’est ce qu’on appelle la sélection du template :
Création des données pMRP via Top-Level Materials
L’objet de sélection est basé sur le Material Master. C’est-à-dire que le système fera le focus sur les informations matériels en regardant les PIRs du ou des matériel(s) sélectionné(s) afin de déterminer la capacité allouée aux différents Work Centers.
Création des données pMRP via Work Center
L’objet de sélection est basé sur le Work Center. Dans ce cas, le système fera un focus sur le Work Center en regardant les réservations de capacité sur le ou les work center(s) sélectionné(s) et identifiera ensuite les matériels avec leurs PIRs respectifs.
Dans notre exemple, sélectionnons l’option « Creation of pMRP Data via Top-Level Materials » :
Note : il se peut que les templates ne soient pas affichés. Pour résoudre ce souci, rendez vous sur ce lien afin d’établir la configuration technique manquante : Help SAP.
Une fois l’option choisie, le planificateur doit paramétrer les options de planification du job. C’est à cet endroit qu’il détermine si le job doit se lancer immédiatement ou s’il le planifie à une date ultérieure.
Enfin, il faudra configurer les paramètres de sélection qui vont permettra de déterminer les données à prendre en compte lors de la simulation. Ces données vont par conséquent différer en fonction du template sélectionné précédemment.
Après avoir complété les trois sous-étapes de création de la simulation pMRP, vous pouvez planifier le job pour une exécution à la période sélectionnée. Pour vérifier que tout s’est bien déroulé lors de l’exécution du job, il est conseillé de se rendre dans la partie « Application Log » et vérifier le statut du job ainsi que les potentiels messages d’erreurs.
Étape n°2 : Gestion et exécution des simulations pMRP
Désormais, nous allons utiliser la seconde application Fiori Process pMRP Simulations afin de pouvoir gérer les simulations, analyser les résultats de planning, identifier et ajuster les problèmes de capacité ou encore valider les prévisions créées. En premier lieu, l’écran d’accueil de cette transaction permet de lister les différentes simulations effectuées, y compris en affichant le nombre de problèmes de capacité détecté, l’indicateur de performance ou encore le statut de la simulation :
En effet, en cliquant sur une des simulations, nous pouvons accéder à un nouvel écran « Demand Plan Simulation », où nous allons pouvoir analyser en détail et ajuster les résultats de la simulation. Les colonnes en rouge indiquent un problème de capacité sur la période en question. Pour avoir le détail du problème, il suffit de sélectionner la case afin que l’Inspector Panel puisse s’ouvrir sur la droite de l’écran et communiquer au planificateur le détail des problèmes de capacités rencontrés.
Concernant les problèmes de capacités aux niveaux de la charge des postes de travail. Il existe en effet une vue graphique très intéressante qui permet de visualiser graphiquement la charge par période. Le trait horizontal donne la capacité de production maximale, si l’histogramme se trouve en dessous de cette limite, alors il s’agit d’un plan de production faisable et il s’affiche en vert. Dans le cas contraire, si l’histogramme se trouve au dessus, la différence est synonyme de surcharge et est donc affichée en rouge sur le graphique :
Afin de résoudre les problèmes de capacités, le planificateur de production devra analyser puis modifier le plan de demande. La force de la fonctionnalité pMRP est de proposer au planificateur les ajustements nécessaires. Ci-dessous, pMRP propose de diminuer la quantité à produire à 9 PC au mois de Juin afin de solutionner un problème de capacité. Ainsi, en cliquant sur le bouton « Adopt Proposal », le plan s’aligne avec la proposition :
Mais il est également possible d’autoriser une éventuelle surcharge du Work Center en indiquant une nouvelle capacité de charge supérieure à 100%. Tout comme précédemment, pMRP propose ici aussi une juste valeur permettant de solutionner le problème de capacité (Proposed Capacity Utilization à 109%). Le planificateur de production peut décider de s’aligner sur la proposition automatique en cliquant sur le bouton « Adopt Proposal » ou en renseignant une valeur manuellement directement dans la case « New Capacity Utilization » :
Ainsi, une fois les problèmes de capacités résolus, la colonne « Capacity Issues » doit indiquer la valeur « 0 ». En fonction de nombre de pièces à produire qu’il a été décidé de réduire, l’indicateur « Delivery Performance » peut diminuer. Dans notre cas, après correction des problèmes de capacités, notre indicateur Delivery Performance est à 90%. Ainsi, nous produirons 90% de ce qui avait été initialement prévu :
Etape n°3 : Activation des résultats pMRP
Finalement, une fois le plan désiré atteint, il faudra Release la simulation afin de l’envoyer au planning opérationnel. Pour ce faire, il suffit de cliquer sur le bouton « Release » et configurer les paramètres :
Le processus pMRP est ainsi terminé. Vous l’aurez compris, il comprend énormément de fonctionnalités que nous ne pouvons toutes aborder à travers notre article. En effet, ce dernier se veut clair et synthétique. En revanche, si vous avez des questions spécifiques, n’hésitez pas à poster un commentaire. Nous nous ferons un plaisir de vous répondre.
Vous souhaitez améliorer vos compétences SAP ? Vous pouvez accéder à nos formations gratuites, ou opter pour nos parcours premium « Par-delà l’horizon » (débutants SAP) ou « Expert Training Center » (approfondissement).
Pierre Balbinot
Consultant SAP fonctionnel, expert EAM (Enterprise Asset Management) et PP (Production Planning).
Laisser un commentaire