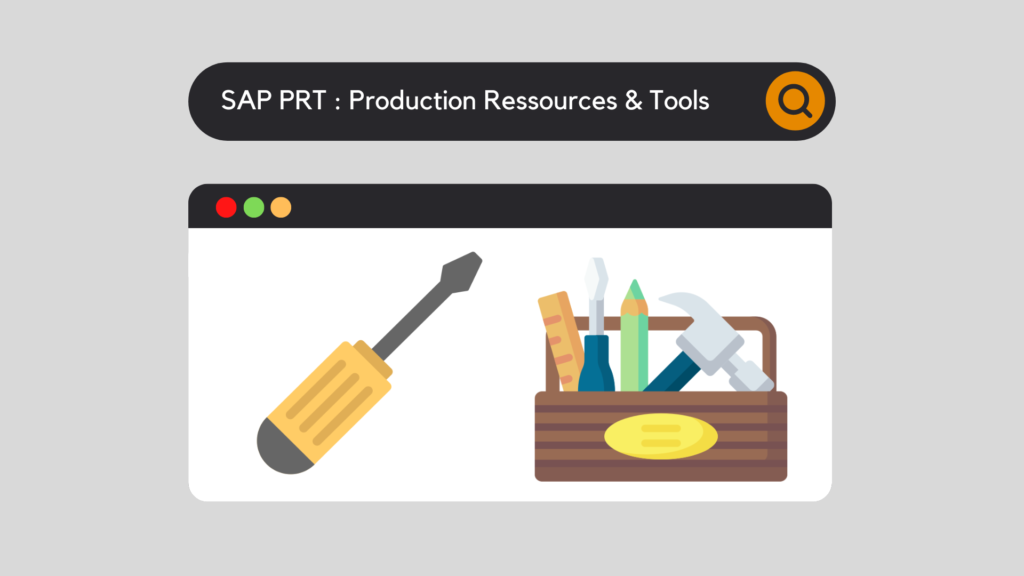
In SAP, there are a multitude of objects, each with their own specific role. Equipment, materials or components are all examples that can be found regularly in SAP. But what is a PRT (Production Resources and Tools)?
Unlike machines or fixed objects, PRTs are mobile elements required to perform a particular operation. Their particularity is that they can be reused several times. To give you some examples, this can represent specific tools, measuring instruments, an industrial design, etc.
Looking at these examples, we can see that there are different types of PRTs. Let's look at them together.
SAP PRT - Categories
In SAP, PRTs are divided into 4 different categories. These will influence their characteristics and use. We distinguish :
PRT Material
First of all, it is considered a material and has its own functionalities. It can be managed in terms of stock, quantity and location. It can also be purchased or produced. It has an additional "PRT" view in its Master Data.
Material Type : FHMI
Miscellaneous PRT
Then, they can be likened to small tools, such as screwdrivers, etc. They are not managed from stock. They are not kept in stock. Nor are they purchased.
Document PRT
Then there are documents that can be used for the chosen operation, such as instructions, technical drawings, etc. They are managed via SAP Document Management. These are managed via SAP Document Management. To find out more, please refer to our dedicated article
Document Type : DRF
To learn more about documents in SAP, I refer you to our dedicated article: SAP DMS Document Management System.
Equipment PRT
Finally, they have the functionality of the equipment used in the PM module. They can be used for internal or external repairs, preventive maintenance, as well as for installation or removal on specific equipment.
Equipment category : P
If you want to find out more about maintenance in general : SAP PM Plant Maintenance Overview
SAP PRT - Overview
It is interesting to see all the possibilities offered by the tools and for our example, we will choose a PRT of type "Material".
PRT material type - creation
The first thing to do is to choose the right type of equipment: Material type FHMI
Then, the second thing is to maintain the data in the PRT view:
- A description of your tools
- The unit of measurement of your tooling.
- Field 3 allows you to exclude or prohibit the use of this tooling on a specific Plant, for specific functions
- Here, we specify under which Task List type a PRT can be used (can it be used only in maintenance? Only in production? Everywhere?).
- These 2 fields allow you to make more precise filters in the selection screens
- With this item, we can inform how the PRT should be processed. Can it be printed, costs allocated, etc.?
- In this way, it is possible to assign a formula which will determine the amount of tooling needed for a given operation.
- The latter, in turn, will assign a formula that will calculate its use, especially for updating counters.
- Determines when the PRT will be used
- Determines when it is not needed
Setting the Grouping Key
SPRO : Plant Maintenance and Customer Service - Maintenance Plans, Work Centers, Task List and PRTs - Production Ressources/Tools - General Data - Define PRT Group Keys
Setting up the Control Key
SPRO : Plant Maintenance and Customer Service - Maintenance Plans, Work Centers, Task List and PRTs - Production Ressources/Tools - Production Ressource/Tool Assignments - Define PRT Control Keys
The formulas
Here we describe in detail how the formulas work and how to use them: Formulas in SAP: tips for a successful configuration.
Material PRT - Good Receipt
Then, of course, to be able to use our tools, they have to be in stock. This is done in the same way as any other material. So you can carry out the MIGO transaction.
Material PRT - Assignment
Now that our items are in stock, let's choose when they will be useful in our process. For SAP, a production resource/tool is used to perform a specific operation. Therefore, it can be assigned in 2 ways:
It can be assigned either in the maintenance module or in the production module. The principle being similar, we will focus together on an example in production.
Let's go into the production Routing
After choosing the operation in question, let's place the PRT.
PRT - Availability check
When material is assigned to an OF, it is possible to check its availability for carrying out the operation, and therefore the OF. The check is carried out :
In case of non-availability, it is then possible to validate the process or to stop it manually, or to carry out this action automatically. The control can be carried out on 2 distinct parameters:
All this is set in the customizing :
SPRO : Plant Maintenance and Customer Service - Maintenance and Service Processing - Maintenance and Service Orders - Functions and Settings for order Types - Availability Check for Material, PRTs, and Capacities - Define Inspection Control
The availability check is then assigned to a particular order type.
- Indicates when the control is carried out. Here, it is triggered at the creation of the Order
- This check box activates or not the availability control for the PRT
- Specify how this control will be carried out (on the basis of status only? Also on the quantity in stock?)
- What happens if the PRT is missing? Is it automatically blocking? Does the user have a choice?
PRT - Status
It is possible to change the status of a tool to prevent its use (in case of breakdown, etc.).
This change is accessible in the Material Master Data, in the Header section.
Finally, once the button has been activated, a padlock appears next to the material:
SAP PRT - Conclusion
Last but not least, the use of tooling / PRT enables greater finesse in the creation of operations, both in maintenance and in production.
What's more, it also lets you assign components that can be reused several times. Coupled with other features such as :
In conclusion, it is possible to be highly efficient and adaptable to most company processes.
Would you like to improve your SAP skills? You can access our free training courses, or opt for our premium "Beyond the Horizon" (SAP beginners) or "Expert Training Center" (advanced) courses.
Michael Antoine
SAP technical-functional consultant, WM (Warehouse Management) and eWM (extended Warehouse Management) expert.
Muhammad Arif Mirza
I would be glad for the participations.
Christian Meisel
Good explaination, very usefull.
But for me not perfect:
the "how to use" of Material PRT description could be a little bit more precise.
What is OF? It's not explained in this course.
keyusertraining@gmail.com
Sorry for "OF" explanation.
It's a Fabrication or Production Order.
The document in SAp to be able to create a finished product based on raw material.
Hope it helps 🙂