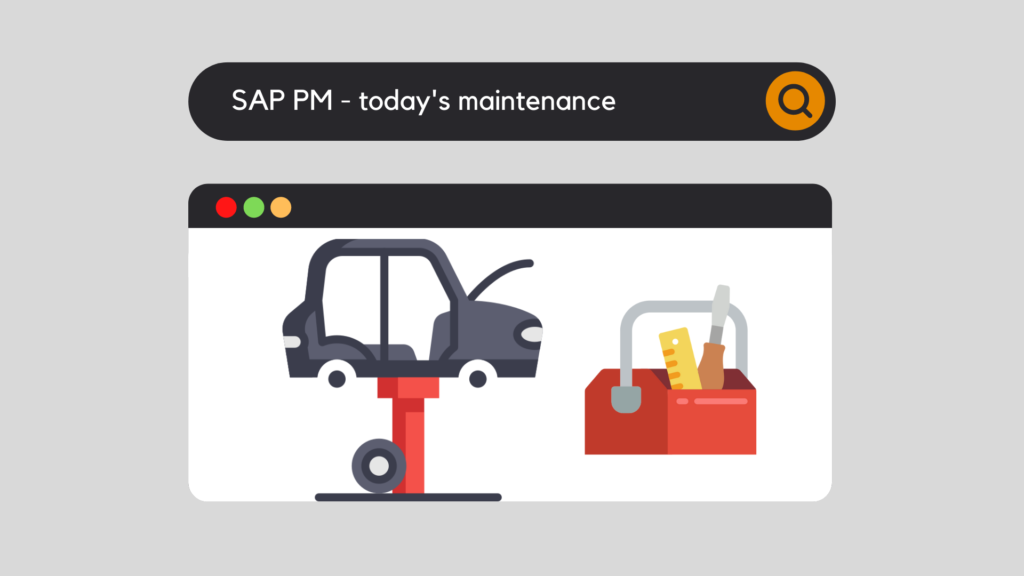
In this article, we will see together what SAP Plant Maintenance is today, its different goals but also, you will understand the right vocabulary to use in the maintenance environment.
This part is important to understand the Plant Maintenance (PM) module of SAP, especially the different technical terms.
More and more companies have abandoned the outdated idea that maintenance is only a cost factor.
The path to competitiveness is increasingly complicated, especially in terms of quality and productivity. Today, we realize that maintenance MUST have a more important place in this race.
The maintenance department is at the heart of the installations, machines, networks, ...
When we want to improve the performance of a company, we can play on several aspects:
Maintenance plays a role in each of the points listed.
It essentially includes the following four tasks:
Inspection
To ensure both high availability and operational safety of machines, technical systems and equipment, regular inspections are necessary to determine their technical condition and define the necessary maintenance tasks.
Maintenance
To achieve the required functional efficiency and availability of machines, technical systems and equipment, you must carry out regular maintenance tasks, based on the manufacturer's guidelines.
Repair
Repair is defined as a set of tasks to restore the functionality of a defective device.
Improvement
Refers to all technical, administrative and management tasks aimed at improving the reliability, maintainability and/or safety of a unit without changing its initial function.
SAP Plant Maintenance: maintenance strategy through time
Technology and evolution have transformed maintenance over time.
Conventional reactive maintenance, which involves repairing the plant after a shutdown, has been successfully replaced by preventive maintenance with a focus on proactive maintenance.
The so-called "fireman's fire" strategy was replaced by increased liaison between plants, as the failure of one machine could stop an entire production line, resulting in high downtime costs.
Preventive maintenance can be time-based (i.e. schedule-based) or performance-based (i.e. counter-based).
SAP Plant Maintenance : Why is this distinction so important?
Performance-based maintenance requires more administrative effort than time-based maintenance.
With time-based maintenance, you define maintenance plans only with fixed or sequential cycles. The maintenance planning and control system can thus calculate all maintenance dates and automatically generate an order for the calculated date.
Performance-based maintenance, on the other hand, requires a counter (kilometers, operating hours, quantities, etc.) and only works properly if counter readings are recorded at regular intervals.
In the beginning, the counter reading was manual and took a lot of time, resources, and was sometimes wrong.
Today, technological advances allow machines to send their own counter linked to the analyzed activity. Industry 4.0, our future already in progress, allows us to be more and more proactive, and to act just in time, reducing errors and costs related to this maintenance.
Would you like unlimited access to our entire SAP training library? Test our training platform free of charge for a 7-day trial period.
Michael Antoine
SAP technical-functional consultant, WM (Warehouse Management) and eWM (extended Warehouse Management) expert.
Leave a Reply