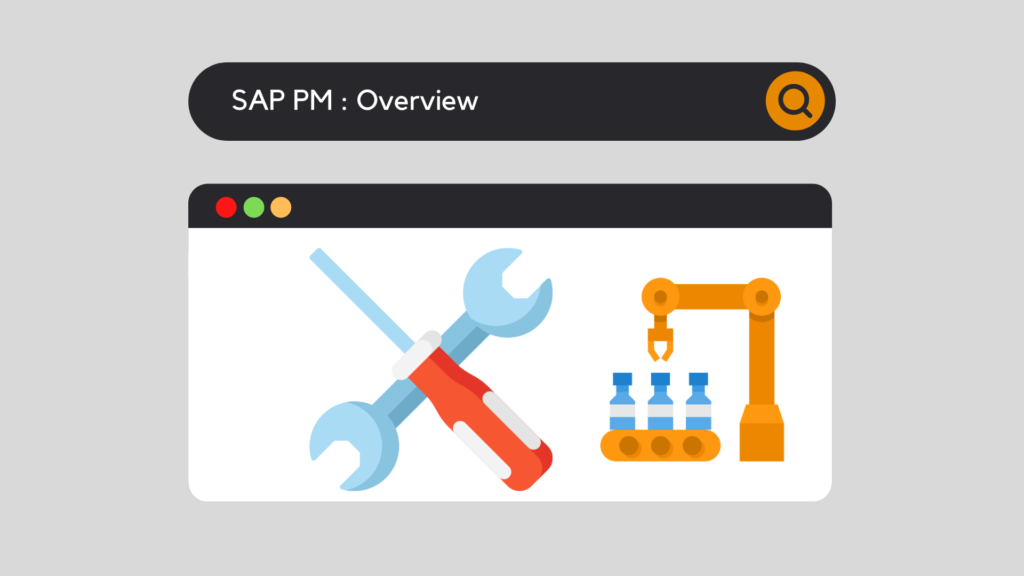
SAP Plant Maintenance : Introduction
Maintenance has become a key element in a world where the competitiveness of companies is omnipresent and where pure productivity is no longer enough. It encompasses a wide variety of functions and varies greatly depending on the industry. To be effective, the maintenance department must rely on management software to manage a large amount of data and interactions between departments, as well as with the outside world. SAP has adapted its SAP Plant Maintenance module to meet this new vision of maintenance in connected industries. This article examines the strengths and limitations of SAP Plant Maintenance to effectively manage the core business. Discover how it works through our presentation of SAP Plant Maintenance - Overview.
SAP Plant Maintenance: Structure and Technical Objects
Firstly, even if maintenance is based on defined processes such as reliability or maintainability, we need to map these processes to a defined structure and the technical objects associated with it.
Note that each company, each entity has its own vision, depending on its leader but also depending on its own context. This is why the SAP plant Maintenance module proposes a multitude of technical objects allowing to adapt to each request, in the smallest details.
Description of the main technical objects
Functional Location
Globally, it represents a complex structure, usually on several levels and vertically. Also, it is used to represent Halls, sections, buildings or processes. Therefore, the equipment will be installed on a Functional Location, allowing to create the tree structure of the plant.
Equipment
It generally represents an individual mobile element. Thus, it can be assimilated to a machine, a means of production such as a pump, a tool or even a robot. Moreover, a piece of equipment will be created when it is necessary to have a history of breakdowns, store information, create notifications or orders, carry out maintenance plans, etc. It will also be possible to manage sub-equipment, which will be attached to the "superior" parent equipment.
Description of technical objects related to a material
PM Assembly
In contrast to an equipment or a functional location, a PM Assembly, which is similar to an item/material, does not describe a single thing but similar elements. Therefore, it usually represents spare parts, assemblies, raw materials, ...
Then, it will be important to define exactly what the PM Assembly should represent in order to define its creation (serialization, material type, ...).
Bill of Material (BOM)
The BOM is a complete and structured set of the components of an equipment or assembly. It also includes the material numbers of each component individually, as well as their quantity and unit of measure. In other words, they can be stored in a central warehouse, or not stored. For assemblies, the BOM is often used to describe them in more detail, so that multi-level structures can be created.
Description of secondary technical objects
Link / Object network
Unlike a Functional Location, which allows to represent a vertical hierarchy, a link allows to establish a horizontal network between several technical objects. To date, a link can be established between 2 pieces of equipment or between 2 Functional Locations. It should be noted that its role is purely informative, but it can nevertheless be used to refine the information when necessary. Take for example the establishment of an electrical network in a factory.
Classification
Indeed, classification is used to describe a group of similar objects based on characteristics they have in common. Thus, it is possible to create classes for grinding machines that would have in common characteristics such as speed of rotation, ... or even classes of furnaces, with characteristics of pressure or temperature.
Special functions attached to technical objects
Note that to go even deeper and allow each user of SAP Plant Maintenance to continuously improve its operation, it is possible to use the following elements :
The business process: SAP Plant Maintenance
Indeed, this part represents the heart of maintenance. The team will map all business processes to those proposed by SAP Plant Maintenance.
Since each company has its own workflows, SAP once again offers various ways to allow everyone to adapt and thus drastically increase performance.
Let's see, right now, some of these accessible processes :
Planned / unplanned repair
Planned and unplanned repair are quite similar. In fact, they occur as a result of an unexpected event.
In reality, the main difference lies in the fact that planned maintenance enables resources to be allocated and intervention to be scheduled over time, but could not be anticipated before the event.
Whereas unplanned maintenance, on the other hand, often refers to a state of emergency, where quick action is required. Thus, it does not involve steps 2 and 3 below, at least the planning part.
Notification is used for several reasons :
Note that this task is essentially assigned to production, allowing maintenance to be called in when necessary.
In this step, the maintenance order is created and planned from the notification. Thus, typical planning tasks are :
In step 3, the analysis goes to the management control. Indeed, it verifies the availability of each part, allowing to realize the intervention in the defined time :
Also, it is at this stage that the various documents will be printed.
After that, the required work will be done. Consequently, the various operations will be carried out and the parts consumed as they progress.
After completing the job, it will then be necessary to consume the last parts used, encode its intervention hours and create a report detailing how the damage was treated.
Finally, there will be a technical confirmation, ensuring that all the previous tasks have been carried out correctly, and then a last step assigned to management control, allowing the maintenance order to be allocated.
External intervention
Externalizing maintenance is extremely important these days for several reasons:
Preventive maintenance
Nowadays, a preventive maintenance strategy is a must in any maintenance department. Although the trend is towards predictive maintenance, we still use most processes, even the most basic ones.
This is why SAP provides a set of tools, allowing to adapt to each level of company, to its progress and its ambitions.
As a result, with regard to the maintenance processes in SAP Plant Maintenance, we find :
Time
This process is characterized by the fact that the interventions are spaced in time, and triggered according to a precise and predefined gap.
We speak then of intervention to be carried out every 6 months, every year, ... based on a company calendar.
Performance
This process, in turn, is not based on well-defined time periods but on counters, predefined characteristics. So that one could, for example, intervene when the machine has reached 2,000 hours of operation.
Condition
The latter process is based on measurement points. These measurement points can be very varied and several can be used for the same technical object. Therefore, one can look at temperature, pressure or even viscosity to trigger a preventive maintenance.
SAP Plant Maintenance: Integration with other modules
SAP's greatest strength lies in the seamless integration between its different modules. Unlike a traditional CMMS that a maintenance department could use and that would probably offer as many functionalities as SAP, its integration with other departments makes it an undeniable leader.
Moreover, the SAP Plant Maintenance module works closely with many other departments within the company. This is why it is necessary to establish a permanent exchange of information between them:
SAP Plant Maintenance: Going Further.
Indeed, modern communication technologies such as the Internet or mobile solutions have now imposed themselves in companies. Especially in the era of Enterprise 4.0, many projects are born, and these technologies, somewhat ignored in the past, are gradually taking a predominant place.
In truth, we will not detail this part which could be the subject of other articles. However, we would like to show you its existence :
SAP Plant Maintenance : Conclusion
After reading this article, you will see that companies really appreciate the maintenance module. Moreover, its impact and importance increases over the years.
Based on this fact, SAP has been able to adapt to the technological evolution and can now offer a whole range of indispensable tools to assist a maintenance department that seeks performance.
So, we have swept together what SAP has to offer you. Mention that the implementation of all these tools remains complex. Nevertheless, if you liked this introduction, you are curious and you want to go further, I refer you to our training dedicated entirely to this module that is SAP Plant Maintenance.
Would you like unlimited access to our entire SAP training library? Test our training platform free of charge for a 7-day trial period.
Michael Antoine
SAP technical-functional consultant, WM (Warehouse Management) and eWM (extended Warehouse Management) expert.
SAP Plant Maintenance - Permits - SAP Training and Coaching
[…] […]